Electrical Thermal Imaging
IR thermography is an efficient, nonintrusive method for identifying potential electrical safety hazards. It reduces the risk of fire while increasing the electrical system's and associated equipment's overall reliability. Using a thermal imaging survey as part of your condition-based monitoring can reduce maintenance costs and downtime. The survey takes place during normal operations, removing the need for a shutdown and keeping your industry at its most profitable.
Electrical Safety
Although commercial and industrial systems undergo EICR electrical installation condition reports every 3-5 years, under the Electricity at Work Regulations 1989 reg 4(2), interim inspections are also required in addition to the 3-5-year EICR. External influences such as vibration, humidity, mechanical stress, and unbalanced loads can adversely affect an electrical system. When applied as part of a condition-based monitoring system, IR thermography can identify these issues early, before failure occurs.
​
Fire Safety
The leading cause of workplace fires in the UK is faulty or misused electrical equipment, accounting for 25% (IOSH.com). High electrical resistance from poor electrical connections can generate excessive heat, which poses a significant fire risk. However, early detection of such hot spots within an electrical system can significantly reduce the fire risk.
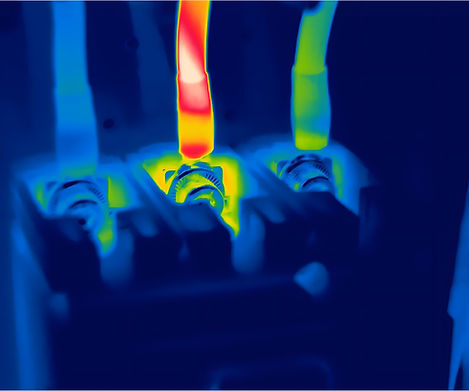
Reduce Maintenance Costs
Condition-based monitoring can significantly reduce the costs associated with replacing components. A rise in the component temperature can often be identified before the increased temperature becomes a critical point and the component is permanently damaged.
In addition to the higher costs linked to reactive maintenance, such as increased component expenses, expedited shipping, and unplanned labour, further savings can be achieved by implementing IR inspections due to the extensive area and greater number of assets that a thermographer can examine compared to other electrical testing methods.
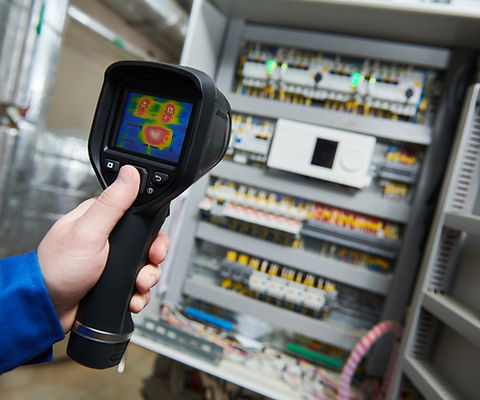
Increase Reliability
A single point of failure can often have a detrimental effect on a whole production site.
Our IR thermography condition-based monitoring can help reduce downtime by identifying issues within your electrical systems before they become critical.
Reduce Energy Consumption
Increased temperature within an electrical system is directly related to increased energy consumption.
Identifying and rectifying unbalanced loads and raised electrical system temperatures will reduce energy consumption.
Remaining Operational During Inspection
IR thermography is a non-destructive testing method (NDT). Unlike an EICR electrical installation condition inspection, thermography inspections are mainly performed on a live/operating system. A minimum of 40% or above loading on electrical components is often preferential.
IR thermography is a safe and efficient method of inspecting-​
Overloaded wiring systems
Internal cable damage
Circuit breakers and fuse holders
PLC components and terminals
Buss bars
Electric motors and controls
Inductive coupling on conductors
Load imbalances
Contactors and switchgear
Insight Thermal Imaging guarantee
Your qualified thermography surveyor will have specific industry experience covering the maintenance and repair of associated equipment.
As a minimum, your surveyor will have gained the following experience and relevant qualifications.
Electrical
-
ITC Certified Thermographer
-
Electro-Technical Level 3 City & Guilds
-
Periodic Inspection & Testing Level 3 City & Guilds
-
ECS/JIB Gold Card
-
IET 18th Edition